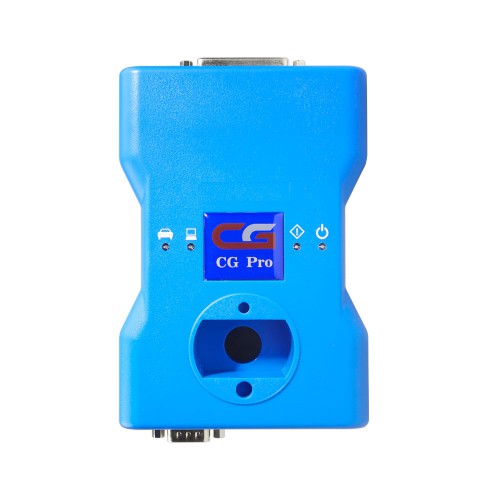
CG Pro 9S12 FAQs
1. How to install the cgpro new device?
Download the latest software from the official website, then connect the device, and plug 12v power cable, the device will automatically be activated.
http://www.cgprogcar.com/en/?c=list&cs=xiazaizhongxi
2. CG pro 35160WT adapter can not erase the chip.
About this may erase 90%, other 10% chip can not be erased. Our development team is improving this adapter. We can send you the new one once we solve this issue.
3. Can CGPRO program car keys?
Yes, You can program keys for BMW, por-sche, land rover and jaguar, find the corresponding anti-theft and then match the keys according to the software tips, if the customer offer us the model which we do not indicate, then cgpro does not support this model.
4. Can cgpro read CAS data?
Yes. But Some BMW CAS anti-theft devices cannot be directly made with obd by CGDI BMW devices. CAS should be removed and then read out with CGPRO, and then loaded into BMW devices. (i.e, CSA3+ CAS4+)
5. Can CGPRO read Mercedes lock data?
Yes. Just like the BMW equipment, CGDI MB cannot be completely lost by obd directly. We also need to remove EIS. CGPRO reads the EIS data and then loads it into the Mercedes equipment.(i.e. W220)
For example many customers will ask how to do W220 all key lost: first with a programmer(our CGPRO 9S12) will lock chip data read out, and then load the data into the CGDI MB, and then do according to the software prompts.
6.Brief description of 35160WT operation:
The erasure of 35160WT consists of two stages. The first stage is to initialize the device (prompt: it takes 5-20 minutes to initialize the device, please wait patiently). The second stage is to erase (prompt: erase time is about 5-40 minutes, please wait a moment…/Erase time of about 5-40 minutes, wait please…). If the device has been initialized, it will go directly to the second stage. Note that the second stage is really the stage of erasing the chip, the first stage is only the adaptation between the host and the chip.
35160WT erase heating method description (if the chip can not be erased can try):
Before operation, adjust the air gun to 100 degrees Celsius and heat the chip for 20-30s (the chip is welded on the board). After that, stop heating and install it immediately to try the operation. If the chip is not erased in the second stage after the chip is completely cooled, it can be reheated by air gun for 20 to 30 seconds and then stopped heating. Chips may be erased during cooling.
7. Cgpro can not erase it if it is more than 800000km.
Yes
8. Why does the car diagnose a fault when some modules have gone through an ICP operation?
Some of the modules on cars are very smart, especially newer cars.When the module is powered up, the program in the module will check whether the voltage and other working conditions at each point are normal.If it is not in the normal state, an error code is written to the EEPROM. However, ICP operation is to remove the module from the car and only power the microcontroller. The level of other ports must be abnormal, so this problem will occur.
So using ICP mode is risky, especially for operating smart module.
9. Why is it that some modules can be read and some modules cannot be read but the microcontroller is the same?
The operating mode out of reset is determined by the states of the MODC, MODB, MODA pins during reset. The MODC, MODB, MODA bits in the MODE register show the current operating mode.
Mode Selection:
1). Normal modes: Some registers and bits are protected against accident changes.
2).Special modes: Allow greater to protected control registers and bits for special purposes such as testing.
Therefore, please measure the MODE pin before operation to ensure that the chip is in normal MODE!
10. Why is the module function still abnormal after writing EEPROM and FLASH data when the master is HC912 series module?
The EEPROM module contains an extra word called SHADOW word which is loaded
at reset into the EEMCR, EEDIVH and EEDIVL registers.
EEMCR—EEPROM Module Configuration $00F0
bit 7 | bit 6 | bit 5 | bit 4 | bit 3 | bit 2 | bit 1 | bit 0 |
NOBDML | NOSHW | RES | RES | 1 | EESWAI | PROTCK | DMI |
NOBDML—Background Debug Mode Lockout Disable
0 = The BDM lockout is enabled.
1 = The BDM lockout is disabled.
Loaded from SHADOW word at reset. Read anytime.
Write anytime in special modes (SMODN=0).
To unlock BDM with storage rest data contents of register please do next:
1) Read register data at address $000F0
2) Set MOST significant bit to ??!!!
For example: If data at address $000F0 contain $79 make logical OR with $80
$79 OR $80 = $F9;
3) Next write this value to EEPROM
4)BDM will be enable after next reset ONLY !!!
NOTE: MC68HC912 without post fix has EEPROM shadow byte only.But it located at the same address $000F0.
11. Why does the chip encrypt after the FLASH data is written and reset?
This FSEC register holds all bits associated with the device security. This register is unbanked.
Flash and security byte address
bit 7 | bit 6 | bit 5 | bit 4 | bit 3 | bit 2 | bit 1 | bit 0 |
KEYEN | NV6 | NV5 | NV4 | NV3 | NV2 | SEC1 | SEC0 |
KEYEN—Enable backdoor key to security.
1 = backdoor to Flash is enabled.
0 = backdoor to Flash is disabled.
NV[6:2]-Non Volatile Flag Bits.
These 5 bits are available to the user as non-volatile flags.
SEC[1:0]-Memory Security Bits.
The SEC[1:0] bits define the security state of the device as shown
in Security states table:
SEC [1:0] | Description |
00 | Secured |
01 | Secured |
10 | Unsecured |
11 | Secured |
The Flash security state is defined by the SEC bits of the FSEC register.During reset, the Flash module initializes the FSEC register using data read from the security byte of the Flash configuration field at global address 0x7F_FF0F.
Flash and security byte address
Flash Size | Description |
32k | 0x7F0F |
64k | 0xFF0F |
128k | 0x1FF0F |
256k | 0x3FF0F |
384k | 0x5FF0F |
512k | 0x7FF0F |
768k | 0xBFF0F |
1024k | 0xFFF0F |
If the byte you want to write FLASH data in the above table for the address is XXXXXX00/ XXXXXX01/ XXXXXX11,then after you have written this data and reset , the microcontroller will encrypt.
12. CG Pro error device is not connected?
Connect CGPro with 12V power supply (it does not have power supply in package, you can use any 12V DC power supply)
Connect CGPro with PC via USB
Run CGPro software